Планирование производственных мощностей бизнес план
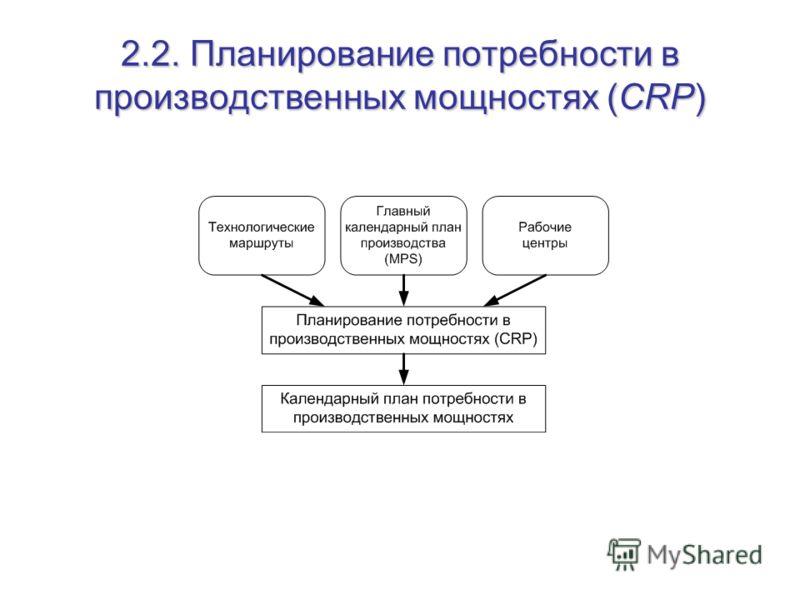
Производственная
мощность –
это показатель, отражающий максимальную
способность предприятия (подразделения,
объединения или отрасли) по осуществлению
выпуска продукции в натуральных или
стоимостных единицах измерения,
отнесенных к определенному периоду
времени (смена, сутки, месяц, квартал,
год).
Количественные
значения производственной мощности
обусловлены научно-техническим уровнем
технологии производства продукции,
номенклатурой (ассортиментом) и качеством
продукции, а также особенностями
организации труда, наличием энергетических,
сырьевых и трудовых ресурсов, уровнем
организации труда, специализации и
кооперирования, пропускной способностью
транспортных, складских и сбытовых
служб. Неустойчивость факторов, влияющих
на величину производственной мощности,
порождает возможность существенного
изменения этого показателя во времени,
и поэтому он подлежит периодическому
пересмотру.
В
общем виде производственную
мощность можно
определить, как максимально возможный
выпуск продукции в соответствующий
период времени при обозначенных условиях
использования оборудования и
производственных ресурсов (площадей,
энергии, сырья, живого труда).
Производственные
мощности измеряются, как правило, в тех
же единицах, в которых планируется
производство данной продукции в
натуральном выражении (тоннах, штуках,
метрах).
По
продукции, имеющей широкую ассортиментную
шкалу, производственные мощности могут
выражаться в условно-натуральных
единицах.
Виды
производственной мощности.
В
связи с этим выделяют следующие
разновидности производственной мощности:
1)
Проектная мощность — определяется в
процессе проектирования производства
и отражает его возможности для принятых
в проекте условий функционирования
предприятия;
2)
Освоенная мощность — это фактически
достигнутая мощность, в результате
устойчивой работы на предприятии;
3)
Пусковая мощность – мощность, сложившаяся
в период пуска производства;
4)
Фактическая мощность — сложившаяся при
текущих колебаниях спроса на продукцию
предприятия;
5)
Плановая мощность — применяемая в
расчетах производства объемов продукции;
6)
Входная и выходная мощность по периоду2– мощность на начало или конец какого-то
временного периода;
7)
Вводимая и выводимая мощность – мощность,
введенная или, соответственно, выведенная
из эксплуатации с начала определенного
периода времени;
8)
Среднегодовая мощность – мощность,
рассчитываемая в случае изменения ее
значения в течение года, как
среднеарифметическое значений
производственной мощности на протяжении
года;
9)
Балансовая мощность – мощность,
соответствующая по своей количественной
мере условиям сопряжения разных по
мощности единиц оборудования, сопряженных
в едином технологическом процессе.
Надо, однако, отметить, что балансовая
мощность не всегда соответствует
оптимальным значениям оборудования;
10)
Резервная мощность – мощность, учитывающая
необходимость остановки оборудования
для профилактических и ремонтных работ
на предприятии.
Основные
этапы расчета производственной мощности
При
расчете производственной мощности
предприятия, на начало планового года,
должно учитываться все установленное
оборудование, независимо от его состояния
(действует или бездействует вследствие
его неисправности, находится в ремонте,
наладке, в резерве, на реконструкции
или на консервации и т.п.). Резервное
оборудование, предназначенное для
замены ремонтируемого, при расчете
мощности не учитывается.
При
вводе новых мощностей по планам
капитального строительства и их освоения
предусматривается, что их эксплуатация
начинается в следующем квартале после
сдачи.
Входная
и выходная производственная мощность
исчисляются ежегодно по данным отраслевой
статистики, как внешняя конкурентная
характеристика оборудования. Для
определения соответствия производственной
программы имеющейся мощности исчисляется
среднегодовая производственная мощность
предприятия.
Планирование
производственных мощностей.
Планирование
производственных мощностей очень важно
в достижении долгосрочного успеха
организации. Как показывает опыт, слишком
большие производственные мощности
могут быть не менее вредны, чем слишком
маленькие.
Менеджеры
предприятия должны исследовать три
измерения стратегии выбора производственной
мощности перед принятием соответствующих
решений:
выбор
размера запаса производственной
мощности,выбор
времени и размера расширения и связывание
решений по производственной мощности
с другими принимаемыми решениями.
Запас
производственной мощности –
это количество дополнительной
производственной мощности, которую
фирма сохраняет, чтобы справиться с
внезапными увеличениями в спросе или
временными потерями в производительности;
она измеряет насколько средний уровень
использования (в терминах реальной
производственной мощности) меньше 100
процентов.
Выбор
времени и размера расширения. Вторая
проблема стратегии производственной
мощности состоит в том, чтобы определить:
когда ее расширять и насколько. Существует
две крайние стратегии: экспансионистская
стратегия, которая добавляет
производственную мощность большими,
но редкими порциями, и стратегия
wait-and-see
(«ждать и смотреть» или «поживем-увидим»),
которая делает эти добавки меньшими
порциями, но более часто. В первом случае
производственная мощность наращивается
заблаговременно (когда заканчивается
ее запас), а во втором случае – тогда,
когда ее дефицит достигнет определенного
порога.
Планирование
ввода дополнительных производственных
мощностей рекомендуется осуществлять
по следующим этапам.
1.
Оценить требуемую производственную
мощность.
2.
Вычислить разницу между требуемой и
доступной производственной мощностью.
3.
Составить варианты планов ликвидации
разрыва.
4.
Качественно и количественно оценить
каждую альтернативу и сделать окончательный
выбор.
Система
планирования производственных мощностей
по методологии CRP применяется для
проверки пробной программы производства,
созданной в соответствии с прогнозами
спроса на продукцию, на возможность её
осуществления имеющимися в наличии
производственными мощностями. В процессе
работы CRP-системы разрабатывается план
распределения производственных мощностей
для обработки каждого конкретного цикла
производства в течение планируемого
периода. Также устанавливается
технологический план последовательности
производственных процедур и, в соответствии
с пробной программой производства,
определяется степень загрузки каждой
производственной единицы на срок
планирования. Если после цикла работы
CRP-модуля программа производства
признается реально осуществимой, то
она автоматически подтверждается и
становится основной для MRP-системы. В
противном случае в неё вносятся изменения,
и она подвергается повторному тестированию
с помощью CRP-модуля. В дальнейшем
эволюционном развитии систем планирования
производства они стали представлять
собой интеграцию многих отдельных
модулей, которые, взаимодействуя,
увеличивали гибкость системы в целом.
Структура CRP-систем.
Планирование
потребности в производственных
мощностях осуществляется по каждому
виду продукции, включенного в главный
календарный план. При планировании
учитывается последовательность
выполнения технологических операций
изготовления продукции на рабочих
центрах.
Capacity
Requirements Planning (CPR)
— Планирование производственных
мощностей. Информационная система,
входящая в состав более крупных систем
MRP. Цель CRP-системы -проверка выполнимости
заданного графика работ с точки зрения
имеющегося оборудования и возможностей,
и в случае адекватности требований и
возможности выполнения задания по
срокам оптимизировать и грамотно
распределить нагрузку на имеющиеся
производственные ресурсы.
Рис.2.15.
Цикл CRP
В
процессе работы CRP-системы разрабатывается
план распределения производственных
мощностей для обработки каждого
конкретного цикла производства в течение
планируемого периода. Также устанавливается
технологический план последовательности
производственных процедур и, в соответствии
с пробной программой производства,
определяется степень загрузки каждой
производственной единицы на срок
планирования. Если после цикла работы
CRP-модуля программа не признается реально
осуществимой, то в нее вносятся изменения,
и она подвергается повторному тестированию
с помощью CRP-модуля.
В
CRP-алгоритме можно условно выделить два
этапа. Речь идео об предварительном и
окончательном планировании:
RCCP
(Rough-Cut Capacity Planning).
Предварительное
планирование производственных мощностей.
Процедура достаточно быстрой проверки
нескольких ключевых ресурсов, с помощью
которой можно выяснить, достаточно ли
мощностей для выполнения основного
плана производства.FCRP
(Finite Capacity Resource Planning).
Окончательное
планирование производственных мощностей.
Даже если RCCP может указывать на наличие
достаточного объема мощностей для
выполнения плана производства, FCRP может
показать дефицит этих мощностей в
определенные периоды времени.
Для
каждого рабочего центра рассчитывается
плановая загрузка, учитывается
ограничение производственной мощности,
выдается сообщение обо всех расхождениях
между их плановой потребностью (загрузкой)
и имеющейся мощностью. Это позволяет
своевременно предпринимать регулирующие
действия, направленные на выравнивание
загрузки рабочих центров за счет
перераспределения потоков операций
или, в крайнем случае, за счет изменения
производственной программы. При этом
системы CRP не
обеспечивают оптимизацию загрузки
рабочих центров, оставляя эту
интеллектуальную процедуру человеку.
В результате получается производственная
программа, которая соответствует
реальным возможностям загрузки
рабочих центров — производственным
мощностям. Эта производственная программа
становится основной для планирования
материальных потребностей в MRP-системе.
Для
планирования потребности производственных
мощностей используют исходные данные:
• календарного
плана производства (сведения о
производственных заказах);
• о
рабочих центрах (состав, рабочий
календарь, производственная мощность
рабочих центров);
• о
технологических маршрутах изготовления
готовой продукции.
Типовая
структура информационной базы,
поддерживаемая большинством
программных продуктов ИС класса CRP,
приведена на рис. 4.3. Недостатком CRP-систем
является учет ограниченного перечня
производственных факторов, а также
отсутствие средств моделирования и
оптимизации загрузки рабочих центров.
Рис.
2.16. Типовая структура информационной
системы класса CRP
Информационные
системы классов CRP/MRP обеспечивают
реализацию функций управления в
направлении «сверху вниз», без учета
обратной связи, а также решение
функциональных задач планирования
потребностей в материалах и производственных
мощностях.
Такие
функции управления, как бизнес-планирование,
планирование продаж, планирование
производства, разработка главного
календарного плана производства,
оказались не охваченными ИС классов MRP/CRP.
Для
того чтобы производственная программа
была осуществима, необходимо, чтобы
имеющиеся в наличие производственные
мощности смогли обработать то количество
сырья и материалов-комплектующих,
которое предписывает составленный MRP
модулем план заказов, и изготовить из
них готовые изделия. Собственно MRP-план
является основным входным элементом
модуля планирования потребностей в
производственных мощностях (CRP-модуля).
Другим немаловажным входным элементом
является технологическая
схема обработки/сборки конечного
готового изделия (routing plan).
Эта схема является определенной таблицей,
аналогичной инвентарному списку, только
с точки зрения этапов обработки и их
длительности, а не комплектующих и их
количества. На рисунке 5 представлена
типичная технологическая схема обработки.
Обычно, производственные мощности
предприятия классифицируются на
производственные
единицы (work center).
Такой производственной единицей может
быть станок, инструмент, рабочий и т.д.
Результатом работы CRP-модуля является
план
потребности в производственных мощностях
(Capacity requirements plan).
Этот план определяет, какое количество
стандартных часов должна работать
каждая производственная единица, чтобы
обработать необходимое количество
материалов.
Шаг | Номер | Название | Название | Кол-во |
1 | 456676 | Расточка | Токарный | 1 |
2 | 56787, | Шлифовка | 5 | |
2.1 | 56787 | Станочн. | Шлифовальный | 4 |
345 | Ручн | Рабочий | 1 | |
…. | …. | … | … |
Рис
2.25.
Технологическая схема обработки/сборки
готового изделия (routing plan)
Также
очень важно заметить, что модули
MRPII-системы являются четко и однозначно
взаимосвязанными (Lock step principle).
Это в свою очередь означает собой тот
факт, что в любом случае, если потребности
в материалах (MRP-план, являющийся
следствием изначально составленной
программы производства (MPS)) не могут
быть удовлетворены ни за счет внутреннего
производства, ни за счет закупок на
стороне, в план производства, очевидно,
должны быть внесены изменения. Однако
подобные явления должны быть исключениями.
Одной из основных задач является
составление успешного производственного
плана с самого начала.
На
Рис. 2.26 представлен сокращенный вариант
типичного плана потребности в
производственных мощностях. Этот план
является выходным элементом CRP-модуля.
План | ||||||||||||
Номер | Номер | Кол-во | 1.03.99 | 2.03.99 | 3.03.99 | 4.03.99 | 5.03.99 | |||||
91234 | 12378 | 50 | 3.5 | |||||||||
80902 | 9870 | 500 | 16.5 | |||||||||
Суммарное | 294 | 201 | 345 | 210 | 286 |
Рис.
2.26. План потребности в производственных
мощностях на примере одной производственной
единицы.
Таким
образом, заметим еще раз: если в результате
работы CRP-модуля установлено, что MRP-план
неосуществим, то производственная
программа (MPS)
должна быть пересмотрена, более того,
вероятно, необходимо пересмотреть весь
план деятельности. Однако важно
осознавать, что такой шаг должен быть
сделан в самом крайнем случае, так как
планировщик, работающий с CRP-системой
должен быть компетентен и сам осознавать
производственные возможности своего
предприятия, понимая, что задача
компьютера — лишь оптимально распределить
загрузку производственных мощностей
на период планирования. Тем самым,
планировщик должен стараться определить
и опротестовать заведомо неосуществимый
MRP-план, до отправления его в CRP-систему,
или найти пути для расширения
производственных мощностей до необходимого
уровня.
Контроль
выполнения производственного плана.
Контрольные отчёты по производительности
и потреблению (input/output reports)
В
тот момент, когда определено, что план
потребностей в производственных
мощностях может быть осуществлен,
начинает функционировать контроль
поддержания установленной производительности.
Для этого в течение всего срока
планирования системой регулярно
создаются контрольные отчеты по
производительности (Output control reports). Пример
такого отчета приведен на рисунке 7.
Контрольный Единица | ||||
Статус/Дата | 2.05.99 | 9.05.99 | 16.05.99 | 23.05.99 |
По | 270 | 270 | 270 | 270 |
Реально | 250 | 220 | 190 | |
Отклонение | -20 | -70 | -150 |
Рис.
2.27. Пример контрольного отчета по
производительности. Установленный
период создания отчетов — 1 неделя.
Из
вышеприведенного контрольного отчета
становится видно, что отклонение
реального темпа производства от
производственного плана в первую неделю
составляло 20 часов, во вторую-50 и в третью
— 80 часов работы. Таким образом, суммарное
отклонение достигло 150 стандартных
часов.
Для
адекватной работы системы необходимо
определить величину допустимого
отклонения от плана производства.
Например, если установлено, что величина
допустимого отклонения на начало третьей
недели равна половине планового
недельного количества часов, то для
примера на рисунке 7 это отклонение
будет равняться 135 часам. И, в тот момент,
когда величина реального отклонения
превышает 135 часов, система сигнализирует
о необходимости немедленного вмешательства
в работу данной производительной
единицы, и принятия мер к повышению ее
производительности, вплоть её выхода
на плановый уровень. Такими мерами может
быть привлечение дополнительных рабочих,
допустимое увеличение общего времени
её работы и т.д.
Кроме
контрольных отчетов производительности,
для каждой производительной единицы
существуют контрольные отчеты потребления
материалов-комплектующих. Эти отчеты
существуют для быстрого определения
ситуаций, когда та или иная производительная
единица не развивает плановой мощности
из-за недостаточного снабжения
материалами.
Еще
одним необходимым документом, регулярно
(как правило, ежедневно) создаваемым
MRPII-системой является список операций
(operation lists). Списки операций обычно
формируются в начале дня и передаются
(или пересылаются) мастерам соответствующих
производственных цехов. В этих документах
отображена последовательность проведения
рабочих операций над сырьем и комплектующими
материалами на каждой производственной
единице и их длительность. Списки
операций позволяют каждому мастеру
получать актуальную информацию, и
фактически делают его частью MRPII-системы.
Соседние файлы в предмете [НЕСОРТИРОВАННОЕ]
- #
- #
- #
- #
- #
- #
- #
- #
- #
- #
- #
9. Планирование производственной мощности предприятия
Возможность предприятия производить определенную продукцию в определенных размерах характеризуется производственной мощностью.
Производственная мощность – максимально возможный годовой объем производства продукции, рассчитанный на основе полного использования всего установленного оборудования, полного использования времени его работы в течение года при применении технических норм производительности оборудования и современной организации производства и труда, т. е. при оптимальном использовании всех факторов, определяющих выпуск продукции.
Производственная мощность служит для обоснования реальной производственной программы предприятия. Производственная мощность рассчитывается только в натуральных и условно-натуральных единицах измерения.
Расчет ведется только по выпускному оборудованию основных производств (отдельно по каждому производству) для всего ассортимента.
Планирование производственной мощности основано на учете факторов, от которых зависит ее величина. При расчете мощности принимаются во внимание следующие факторы: структура и величина основных производственных фондов; качественный состав оборудования, уровень физического и морального износа; передовые технические нормы производительности оборудования, использование площадей, трудоемкости изделий, выход продукции из сырья; степень специализации; режим работы предприятия; уровень организации производства и труда; фонд времени работы оборудования; качество сырья и ритмичность поставок.
Производственная мощность – величина непостоянная. Снижение мощности происходит по следующим причинам: износ оборудования; увеличение трудоемкости изготовления изделий; изменение номенклатуры и ассортимента выпускаемой продукции; уменьшение фонда времени работы; окончание срока лизинга оборудования.
Планирование производственной мощности заключается в выполнении комплекса плановых расчетов, позволяющих определить: входную мощность; выходную мощность; показатели степени использования мощности.
Входная мощность определяется по наличному оборудованию, установленному на начало планового периода. Выходная мощность – мощность на конец планового периода, рассчитываемая на основе входной мощности, выбытия и ввода мощности в течение планового периода.
Планирование выпуска продукции осуществляется исходя из среднегодовой мощности (Мс), рассчитываемой по формуле:
Мс = Мн + Му (Ч1 / 12) + Мр (Ч2 / 12) + Мун (Ч3 / 12) – Мв ((12 – Ч4) / 12
где Мн – производственная мощность на начало планируемого периода (года);
Му – увеличение мощности за счет организационных и других мероприятий, не требующих капитальных вложений;
Ч1, Ч2, Ч3, Ч4 – соответственно число месяцев работы мощности;
Мр – прирост мощности за счет технического перевооружения, расширения и реконструкции предприятия;
Мун – увеличение (+), уменьшение (-) мощности в связи с изменением номенклатуры и ассортимента продукции, поступлением промышленно-производственных фондов от других предприятий и передачи их другим организациям, включая лизинг;
Мв – уменьшение мощности за счет ее выбытия вследствие ветхости.
Следующая глава >
Похожие главы из других книг:
125. Планирование финансовых отношений внутри предприятия. Финансовый раздел бизнес-плана
Финансовые отношения предприятий состоят из четырех групп. Это отношения:— с другими предприятиями и организациями;— внутри предприятия;— внутри объединений, которые включают
4.7. Начисление амортизации на мобилизационные мощности
С 1 января 2006 года не нужно начислять амортизацию на мобилизационные мощности, то есть на те основные средства, которые используются организацией для реализации законодательства РФ о мобилизационной подготовке и
23. Планирование в системе управленческого учета предприятия
Одной из важнейших функций управления на предприятии является планирование.Среди основных принципов планирования можно выделить: 1. Непрерывность – планирование должно осуществляться постоянно, без
2. Организационные типы построения производственной структуры предприятия
Для осуществления производственных процессов на предприятиях создаются основные и вспомогательные цеха и обслуживающие хозяйства.Расчленение предприятия на производственные подразделения
3. Пути повышения эффективности производственной структуры предприятия
Каждому этапу развития промышленности соответствует определенная производственная структура предприятия, которая во многом способствует повышению эффективности его работы.На начальном этапе
ЛЕКЦИЯ № 11. Планирование деятельности предприятия
1. Сущность планирования
Планирование – это разработка и установление руководством предприятия системы количественных и качественных показателей его развития, в которых определяются темпы, пропорции и тенденции
8. Разработка производственной программы предприятия. Этапы разработки производственной программы
Производственная программа – план производства и реализации продукции по объему, ассортименту и качеству.Главная задача при составлении плана производства –
45. Разработка производственной / программы предприятия. Этапы разработки производственной программы
Производственная программа – план производства и реализации продукции по объему, ассортименту и качеству.Главная задача при составлении плана – подтвердить
46. Планирование производственной мощности предприятия
Производственная мощность – максимально возможный годовой объем производства продукции, рассчитанный на основе полного использования всего установленного оборудования, полного использования времени его работы
Глава 2
Как Toyota стала лучшей производственной компанией мира: история семьи Тоёда и производственной системы Toyota
Я намерен свести к минимуму потери времени в технологических процессах и при поставке деталей и материалов. Мой ориентир – подход «точно вовремя». Мое
Глава 2 Планирование развития предприятия
1. Таблица производственной мощности по изготовлению деталей
Чтобы определить стандартные операции, нужно сначала заполнить таблицу производственной мощности по изготовлению каждой детали для каждого процесса.В этой таблице нужно указать следующее:
Избыточные мощности в мире
Проблема стремительной экономической экспансии, произошедшей в мире в 90?х годах XX в., заключается в том, что сегодня предложение большинства продуктов избыточно. Производители всего мира, но особенно азиатские, построили слишком много
Мощности, их место расположения и проектирование
Следующий шаг разработки операционной системы связан с принятием решений относительно операционных мощностей, их расположения и проектирования. Термин мощности весьма широк, он охватывает заводы, фабрики, склады,
Глава 4
Стратегическое управление и планирование инновационной деятельности научно-производственного
5.4. Проектирование производственной стратегии научно-производственного предприятия
Производственная стратегия, являясь одной из функциональных стратегий НПП, представляет собой совокупность детально разработанных долгосрочных планов и мероприятий по созданию и